Iot Remote Asset Monitoring Solution What is IoT Remote Monitoring?
The landscape of manufacturing is evolving rapidly, driven primarily by technological advancements. Among these advancements, IoT connectivity solutions for manufacturing automation stand out as pivotal elements reshaping how industries function. The Internet of Things (IoT) integrates digital and bodily worlds, making a community of interconnected gadgets that talk seamlessly. This interconnectedness permits producers to optimize their processes and improve productiveness.
Real-time knowledge is a cornerstone of recent manufacturing. Through IoT connectivity options, machines and sensors generate knowledge that present insights into manufacturing processes. This quick entry to info empowers producers to make informed choices shortly. For occasion, if a machine is underperforming, operators can determine the problem and implement corrective actions at once, finally minimizing downtime and enhancing throughput.
Iot Revolution Technologies Guide to Real-Time IoT Monitoring
Predictive maintenance is another vital benefit of IoT connectivity options. By continuously monitoring gear efficiency by way of quite a few sensors, manufacturers can anticipate failures before they occur. This proactive strategy drastically reduces maintenance prices and improves the lifecycle of equipment. Instead of adhering to a reactive maintenance technique, organizations can optimize their maintenance schedules based on actual machine circumstances.
IoT know-how additionally facilitates higher supply chain administration. With the combination of sensors all through the supply chain, manufacturers acquire enhanced visibility into stock ranges and materials flows. This improved visibility permits companies to optimize stock management, guaranteeing that they have the necessary materials available without overstocking. Such effectivity interprets to reduced costs and improved service ranges, that are essential for sustaining a aggressive edge.
Remote Monitoring Non-Invasive Devices for IoT Monitoring
Automation and robotics are more and more reliant on IoT connectivity options. Smart factories integrate automated methods powered by IoT to streamline manufacturing processes. Robotics equipped with IoT capabilities can talk with one another and adjust their actions based mostly on real-time knowledge from the environment. This stage of synchronization enables the implementation of adaptive manufacturing techniques that reply to fluctuations in demand quickly and successfully.
Implementing IoT connectivity solutions requires a solid community infrastructure. Manufacturers should put money into dependable and secure communication networks able to dealing with the immense data generated by interconnected gadgets. 5G technology is emerging as a crucial enabler of IoT connectivity in manufacturing. Its fast velocity and low latency support the real-time purposes that are essential for data-driven decision-making.
Remote Monitoring Using Iot Examples of Industrial IoT Monitoring
Data analytics performs an important position in harnessing the total potential of IoT connectivity solutions. With a wealth of data generated from related devices, producers must make use of superior analytics tools to extract actionable insights. Machine studying algorithms can determine patterns and anomalies in information that is most likely not apparent to human analysts. This data-driven approach enhances operational efficiency by driving continuous improvement across manufacturing processes.
Cybersecurity is a vital consideration as manufacturers combine IoT solutions into their operations. The connectivity that IoT brings increases the surface space for potential cyberattacks. Implementing sturdy security measures to safeguard crucial manufacturing techniques is paramount. This entails making certain that every one units are secure, data is encrypted, and continuous monitoring for threats is in place.
Remote Monitoring Basics of IoT Remote Monitoring
Worker safety is significantly improved via IoT connectivity options. Wearable gadgets geared up with sensors can monitor the health and safety of staff in actual time. These smart wearables can alert personnel to hazardous conditions, ensuring well timed intervention. Such measures not solely protect workers but also contribute to general productivity by minimizing the chance of accidents.

The transition to smart manufacturing via IoT connectivity solutions additionally promotes sustainability. By optimizing processes, manufacturers can considerably reduce waste and energy consumption. IoT gadgets assist monitor useful resource utilization, enabling businesses to establish areas the place effectivity could be enhanced. These environmentally pleasant practices not only benefit the planet but also can lead to cost savings over time.
The impact of IoT connectivity options on manufacturing extends beyond the operational realm. They allow enhanced customer engagement by allowing producers to ship custom-made products and services. Through IoT-enabled gadgets, producers can gather information about customer preferences, resulting in the creation of tailored choices that better meet market calls for. This level of engagement fosters customer loyalty and strengthens model status.
It Remote Monitoring Software Benefits of IoT Remote Monitoring
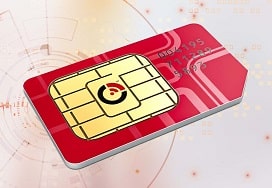
In conclusion, IoT connectivity solutions for manufacturing automation characterize a transformative drive in the business. By offering real-time insights, predicting equipment failures, improving supply chain management, and enhancing employee safety, these solutions redefine operational efficiency. As producers proceed to integrate IoT technologies, the benefits prolong past conventional metrics of productivity and value. Embracing these improvements units the groundwork for a more sustainable and responsive manufacturing environment that is outfitted to satisfy the challenges of the lengthy run.
- Enhanced real-time monitoring by way of IoT sensors permits manufacturers to track machinery performance and operational efficiency.
- Predictive maintenance is facilitated by IoT connectivity, reducing downtime and increasing gear lifespan via well timed interventions.
- Seamless integration of IoT units throughout production strains enhances knowledge assortment, resulting in improved decision-making processes.
- Wireless technologies similar to LPWAN allow cost-effective communication over huge manufacturing services, minimizing set up complexity.
- Cloud-based IoT platforms provide scalable solutions for knowledge analytics and visualization, empowering manufacturers to identify trends and optimize workflows.
- Enhanced asset tracking using IoT gadgets ensures higher inventory administration and reduced losses as a end result of misplacement or theft.
- Industry-specific IoT protocols, like MQTT and CoAP, ensure environment friendly and safe information transmission tailor-made to manufacturing needs.
- Advanced cybersecurity measures are crucial in IoT ecosystems to protect sensitive operational data from potential threats and breaches.
- Integration of IoT with machine learning algorithms permits for autonomous changes and improvements in production processes based on historic information.
- Collaboration with IoT answer suppliers permits producers to customize connectivity strategies that address their distinctive operational challenges.
What are IoT connectivity solutions for manufacturing automation?
IoT connectivity options enable seamless communication between machines, sensors, and units within a manufacturing environment, facilitating information change, monitoring, and control to enhance operational effectivity and decision-making.
How do IoT connectivity options improve manufacturing processes?
It Remote Monitoring Software Guide to Real-Time IoT Monitoring
These solutions streamline workflows, scale back downtime, and optimize asset utilization by offering real-time knowledge insights, enabling predictive maintenance, and enhancing supply chain visibility.
What kinds of IoT connectivity technologies are generally utilized in manufacturing?
Common technologies embrace Wi-Fi, Zigbee, LoRaWAN, cellular (4G/5G), and Bluetooth. Each expertise presents unique benefits based on range, data transfer speed, and energy consumption fitted to different manufacturing needs.
It Remote Monitoring Software Protecting IoT Devices through Monitoring
How secure are IoT connectivity options for manufacturing?
Robust safety measures, including encryption, device authentication, and community segmentation, are essential to guard production environments from cyber threats, ensuring information integrity and operational continuity.
Can IoT connectivity options be integrated with existing manufacturing systems?
- Iot Remote Monitoring And Control
Yes, many IoT options are important source designed for interoperability, permitting integration with legacy systems and equipment. This enables manufacturers to enhance their capabilities without replacing existing infrastructure.
Role Of Smart Sensors In Iot Basics of IoT Remote Monitoring

What are the cost implications of implementing IoT connectivity solutions?
Initial setup costs could differ, but long-term financial savings are sometimes realized through elevated efficiency, reduced waste, and improved maintenance methods. A detailed cost-benefit analysis can help decide the financial impression. It Remote Monitoring Software.
How can I choose the proper IoT connectivity solution for my manufacturing facility?
Evaluate elements corresponding to scalability, reliability, ease of integration, and particular use case requirements. Consulting with business consultants and conducting pilot tasks might help in identifying one of the best match in your needs.
Remote Iot Monitoring Solution Examples of Industrial IoT Monitoring
What are the challenges in adopting IoT connectivity options for manufacturing?
Challenges might embrace cybersecurity considerations, interoperability issues, and the need for employees coaching. Addressing these obstacles by way of strategic planning and stakeholder involvement can facilitate profitable adoption.
How does knowledge collected through IoT connectivity affect decision-making in manufacturing?
Real-time information analytics permits producers recommended you read to make informed selections quickly, optimizing operational processes, enhancing high quality management, and enabling proactive administration of sources and potential issues.